Why did my dangerous goods shipment get rejected? Common causes of rejection and some suggestions to avoid them
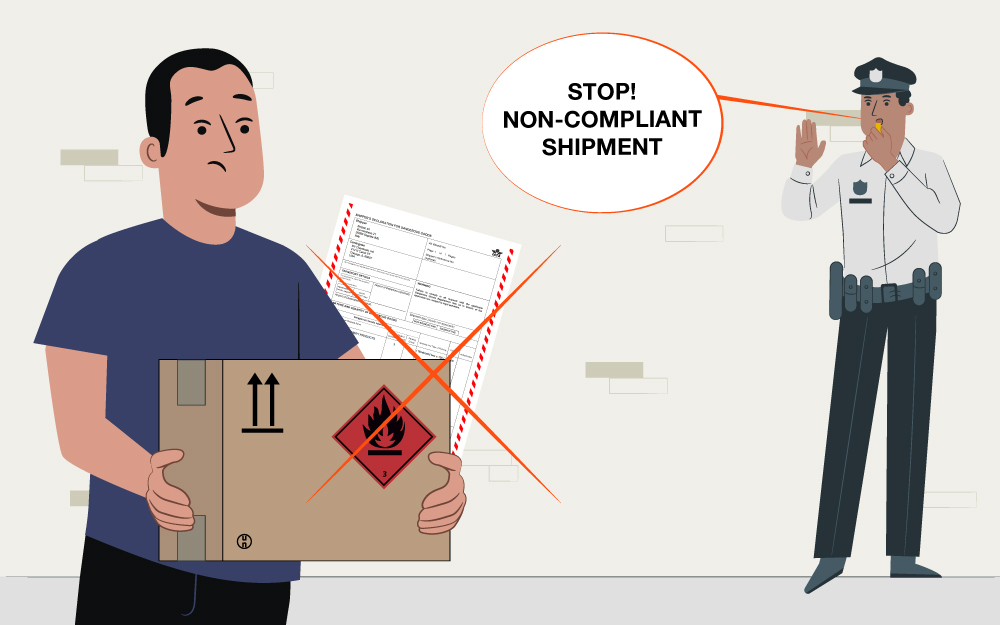
True, maybe not so often, but everyone have had or may have their shipment of dangerous goods rejected by the carrier for some reason. When this happens, your team has to spend valuable time repackaging, relabelling, rewriting paperwork, or otherwise correcting mistakes (big and small).
The consequences are not just on the shipping side; in fact, rejected and delayed shipments disrupt logistics, stall your operations, and can severely impact both your company and your customers.
Undeclared dangerous goods shipments
Knowing which materials are regulated and classified as dangerous goods for transport -and which are not- is the first step toward properly preparing goods for transport. It very often happens that undeclared dangerous goods are presented for transport and this, even if in good faith, can put the supply chain and those involved in transport at risk. If a dangerous material is presented as non-dangerous, the carrier may notice this during the acceptance check and reject the shipment.
This happens in several ways, one of them being product descriptions that trigger suspicion. Another case is when the packaging is accepted and, for whatever reason, breaks during transport (forking, accidental drop, ...). This kind of situation triggers the process of controls, which can be more or less strict, depending on where this incident happens. Also depending on its severity, the incident can lead to inspections that, in some cases, detect the presence of undeclared dangerous goods.
In this case, heavy or less heavy fines may be applied - not to mention that this exposes the various actors involved to potential and harmful risks, one might operate or touch products whose true dangerous nature is unknown.
Avoid these shipping paper mistakes
The shipping paper (shipper, multimodal, …) is one of the most important documents in the dangerous goods shipping process. It’s a certified written record in which you can read what you ship, how much you ship and how it was packed your shipment.
Avoid these easy-to-make shipping paper mistakes to prevent rejection:
- Insert the UN number without the wording “UN”
It is essential to remember that UN numbers should always be preceded by the letters UN; not entering this wording is an error.
- Using an incorrect Proper Shipping Name
When you ship a dangerous good, you must choose the correct Proper Shipping Name (PSN) from the Dangerous Goods Table of the relevant Regulation. An incorrect, unapproved or misspelled PSN can result in rejection of the shipment. - Not listing the quantity and type of package
You must document the type and quantity of packages included in every dangerous good shipment on the shipping papers. For example “3 fibreboard boxes (4G)”. Be careful not to use inappropriate names such as “basket”, “barrel”, “small cans” or “small tanks”.
Use the right packaging
If you offer a dangerous good shipment in a package that is not compatible with the material meant to be shipped or not strong enough to contain it , probably it will be rejected. Authorized dangerous goods packagings bear distinctive markings and your carrier will notice if they are not there or if they don’t correspond to what you are shipping. Be careful, there is important news straight from the IATA Regulation concerning the packaging compliancy.
- X, Y, and Z ratings
Some dangerous goods materials are more “dangerous” than others. Often, a dangerous good material requires a specific strength of package, designated by an X, Y, or Z rating. If the package strength you choose is not correct for your material, your carrier may notice and require repackaging. Beware of the common mistake, people often look for packaging by printed approval and not by the approved contents in that given packaging. It is good to remember that packagings are approved to contain specific products or product categories. A practical example is 4G cardboard boxes as combined packagings. It is certainly essential to verify the packaging group and the approved weight, but it is necessary to know what contents it has been tested for. In practice, if a packaging is not UN-approved for the specific content, it cannot be used - except in special cases or special packaging, e.g. V-packaging. Be careful, always request the test report which should be made available to you.
- Damaged, dented or leaking packaging
This might seem obvious, but if your dangerous goods package is damaged or leaking on the loading dock, your carrier will (and should) reject it. At this point, the control process will be activated to identify the cause.
Non-compliant dangerous goods marks and labels
Dangerous goods labels must be visible, so if they are not made properly, labelling mistakes will be visible as well.
Here are some common marking and labelling mistakes to avoid to ensure acceptance and smooth delivery of your dangerous goods shipments.
- Non-compliant markings or labels
Dangerous goods non-bulk shipments must be marked with different pieces of information. The most important ones are UN number, Proper Shipping Name and the sender and receiver’s address. If this information is not marked on the package properly, you should expect rejections, forced stops and consequent delays. It is good to know that not only design is essential, but also dimensions or the application system. An example? For ADR road transport, dangerous goods labels can be reduced from 100x100 mm down to 50x50 mm, while for IATA air transport, the same labels can be rotated (by placing them in a square, not in a rhombus shape) but, except in special cases, they cannot be reduced; they must have a fixed 100x100 mm size.
- Absurd designs
Inventing new things is not always a good idea, same thing relying on someone who is not in the business. Dangerous goods labels must have a well-defined design, conforming symbols, and appropriate dimensions and materials. Remember, even tenths of a millimetre count especially when your goods pass through northern European countries or are shipped by air.
- Dangerous goods labels too close together or that overlap
The edges of your labels must not overlap or otherwise obscure each other. They must be clearly visible never covered by other labels or by the other information concerning or not concerning the transportation of the dangerous good.
- Labels on more than one side of the package
Dangerous goods labels must be affixed flat on one or more sides of the package. Labels must not "fold" or "bend" over the corner of the package; the whole label must be on one face of the package. - Labels not visible through an overpack
If you use an overpack - for example, four drums wrapped together on a pallet—all labels on all containers must be visible and legible through the overpack. If all labels are not visible, the shipper must reproduce the markings and labels on the outside of the overpack. The advice is to apply the labels and marks on opposite sides of the overpack. - Danger labels too far apart - curiosity
This is more of a curiosity and interest to those shipping to the U.S., as well as the case where their customers reuse the same packaging they received for domestic shipments. If your packaging requires multiple dangerous goods labels (primary and secondary dangers) these should be affixed no more than 15 cm apart.
Critical support for choosing the right products
When every member involved in the supply chain and shipment preparation knows his or her responsibilities for dangerous goods, mistakes can be detected early and rejection of the goods can be avoided. A clear path must be followed by relying on properly trained and educated personnel. Identification and quality of UN approved packaging and dangerous goods labels are always critical points, but for this we at Serpac can support you in identifying the correct product or making it according to your needs and regulatory requirements.